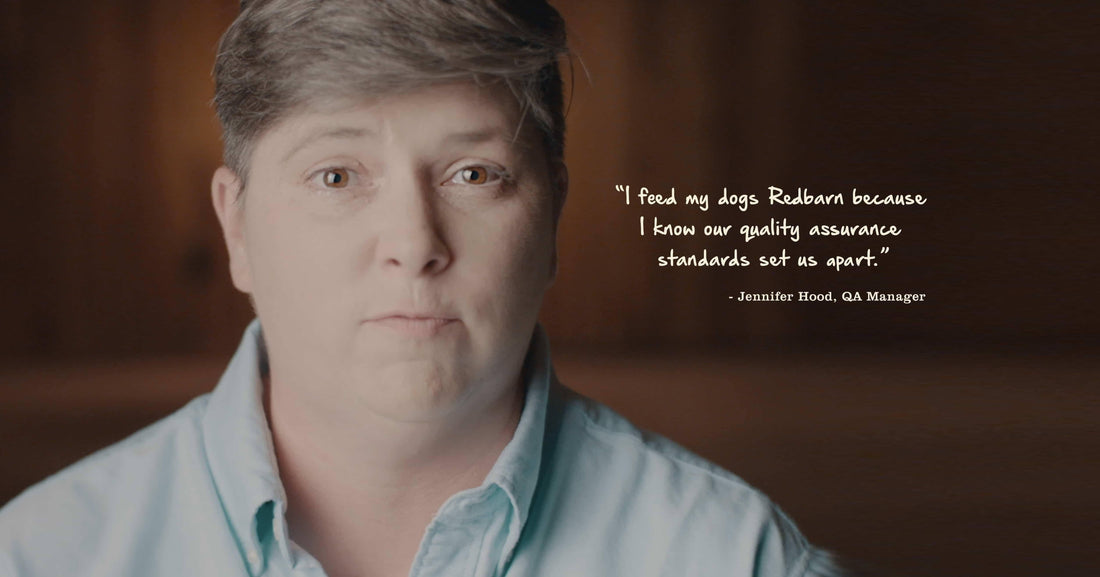
What Does Quality Assurance Really Mean?
Have you ever felt lost walking down the pet food aisle? Perhaps you even left the store empty-handed, overwhelmed by the endless amount of options, most claiming to be healthy, natural, even organic.
It’s important to take a few moments to research what you’re feeding your pet, especially if they’re experiencing any health issues or their breed is prone to certain conditions. Feeding your pet a well balanced and high-quality food is one of the best things you, as a pet parent, can do to fuel a happy and healthy pet.
But how can you be certain you’re picking the best food or treats for your dog or cat if you’re not sure what “quality pet foods” are?
High-quality pet foods should support bodily functions like muscle development, joint health, and bone health; provide a steady stream of energy through natural ingredients and added vitamin and minerals; be easily digestible; help keep their coats and skin shiny and irritant-free; and, even help keep their eyes bright and clear.
Quality food doesn’t stop at ingredient lists and health benefits, though. It also means buying products from companies with leading quality assurance practices, ensuring products are safe for consumption.
But what does quality assurance really mean?
And, how do you know your chosen company is following quality assurance expectations?
The technical definition of quality assurance is the systematic monitoring and evaluation of all raw products that enter and all finished products that exit manufacturing facilities and enter your home. In layman’s terms, quality assurance refers to a series of steps and processes a company puts in place to ensure the final product is safe for consumption.
The main priority of Redbarn’s quality assurance team is ensuring all our products are safe, allowing pet parents to feel confident and secure when selecting Redbarn Pet Products as their food and treat source. As Redbarn’s Quality Assurance Manager, Jennifer Hood, said best, “it’s being a voice for our otherwise voiceless pets.” After all, pets are family, too!
Meet Redbarn’s Quality Assurance Manager
Redbarn believes hiring the most qualified technicians is the first step in building a strong, competent and reliable quality assurance team.
Jennifer Hood is Redbarn’s experienced Quality Assurance Manager. She’s been a Redbarn family member for 4 years, is a HUGE Cubs fan, and, most importantly, is mom to five dogs and two cats— Sandi, Abbie, Junior, Jaxon, Wrigley, Zoey, and Joe!
Jennifer oversees Redbarn’s quality assurance team and has created a robust testing environment for our products and raw materials. She also oversees the Redbarn owned-and-operated QA laboratory, where she runs tests and practices procedures to ensure our food is high-quality and of course, tasty!
Redbarn’s Quality Assurance Labs
Redbarn maintains two state-of-the-art fully equipped labs: one located in Great Bend, Kansas and the other located in Sancay, Paraguay. And before we get too far, while some are understandably wary of non-U.S. manufacturing facilities, it’s important to mention our ownership means we hold both plants to U.S. and Redbarn standards.
Our Kansas lab is fully equipt to test pH, moisture levels, water activity levels, salt levels, and can perform microbiological tests such as aerobic plate counts, anaerobic plate counts, coliform counts, and Salmonella screening. These tests are used to sample raw and finished product. Once all the product arrives in the lab, aseptic laboratory practices are used to prepare and test the products.
Every batch of raw and finished product is tested for quality and safety, with additional samples randomly pulled throughout the production process.
“Redbarn takes pride in doing all of this because we care about you- the pet parent and the safety of your beloved family members,” Hood said.
Our State-of-the-Art Facility Features
From our founding in 1996 through today, Redbarn continues to invest both time and money into our research and quality assurance programs: purchasing state of the art machinery, hiring skilled and educated technicians, and utilizing industry-leading technology and testing protocols.
Temperature Controlled Rooms: Insects can often be a nuisance for pet food manufacturers, especially where bully stick products are made, and a huge concern for pet parents opening infested bags. Our entire manufacturing facility and all testing rooms are temperature-controlled to prevent any insects or harmful toxins from entering the facility.
Food Grade Air Sanitation: Large KES Airocide machines on our ceilings circulate air so no toxins can live within our packaging facility. This machine mineralizes airborne bacteria, mold, fungi, mycotoxins, viruses, allergens, ethylene, and odors.
HACCP: We follow Hazard Analysis and Critical Control Points (HACCP) Standards, a recognized management system in which consumable safety is addressed through the analysis and control of biological, chemical, and physical hazards from the initial raw material production, sourcing, and handling, to the manufacturing, distribution, and consumption of the finished product. This includes multiple required programs specifically designed for our facility and the pet treats and foods we produce. Redbarn’s product and raw material analysis, production and environmental monitoring, and facility audits all support the HACCP program.
Testing
Some of our quality assurance tests include:
-Weekly microbiology tests: Our in-house lab conducts thousands of monthly tests to ensure all products incoming and outgoing are safe for the pet and handling by the pet parent.
-Mold and Yeast Screening: All lots of finished products are tested for yeast and mold.
-Pest Control: We utilize an outside contractor who inspects our facilities weekly.
-Water Specifications: Water activity specifications assure all products and materials cannot support bacterial growth.
-Salmonella Screening: Our team performs and manages around 80 salmonella tests a day. All lots of finished products are screened for salmonella and other bacteria as specified before they are released for distribution.
All of these safety tests add up to a total of 2,5000 tests per month. That’s about 800 tests a week!
Additional Steps in Quality Assurance
We want all pet parents to feel confident feeding their pets Redbarn. We’ve established thorough processes and procedures to ensure the final product you take home is of the highest quality
Internal and External Monitoring
-Surprise USDA and FDA audits: All Redbarn facilities are subject to random audits by the USDA and the FDA.
-Monthly Internal Audits: Our management teams perform monthly internal audits to meet Good Manufacturing Practices (GMP), as well as regularly scheduled audits for food safety and security.
-Independent ISO accredited lab: Redbarn utilizes an ISO accredited lab who verifies our results and ensures we’re doing what we say we’re doing.
Outside Supplier Qualifications
We understand your trust is earned, not given. We not only hold ourselves accountable but our suppliers, as well. As an extension of our family, our suppliers and our globally sourced ingredients are held to the same high standards as our in-house team.
To monitor critical points in our supply chain and ensure our suppliers are delivering high-quality raw materials, we require a Certificate of Analysis from all our suppliers.
This certificate verifies every shipment is pure and the correct grade. And similar to Redbarn, our suppliers are also subjected to surprise audits, where our co-founders and Jennifer Hood visit their facilities to ensure compliance. We won’t package any of our products until our Quality Assurance technicians determine all test specifications are met.
The “Redbarn Guarantee”
Redbarn offers a 100% satisfaction or your money back policy on any and all purchases.
Why?
Because Redbarn is in a committed relationship with quality assurance, and we want to bring peace of mind to our pet parents and retail partners. All of our 200 plus products, from rolled and canned food to Bully Sticks and Filled Bones, are consistently held to these high standards.
“I choose to feed my dogs Redbarn not simply because I work there, but because I know our quality assurance standards set us apart. I want to know raw materials are tested for contaminants before the cooking process begins; I want to have confidence in a company’s standards for cleanliness and safety; I want assurance the finished product is safe for my pets,” Jennifer Hood said. “Safety and quality should be top priorities at every company. We have extensive processes and procedures set in place to ensure all our products are pure, high-quality and consistent.“
Redbarn holds our chews, treats, and food to the highest possible quality standards. Our team works hard to ensure we manufacture safe, high-quality dog and cat food, treats, and chews.
“It’s why we continue to invest both time and money into our research and quality assurance programs: purchasing state of the art machinery, hiring skilled and educated technicians, and utilizing industry-leading technology and testing protocols,” Hood said. “Redbarn takes pride in doing all of this because we care about you- the pet parent and the safety of your beloved family members.”
Quality Assurance FAQs
1. How can pet parents be sure the companies they’re buying from place quality assurance as a top priority?
Research and ask. If you call a company’s customer service line they should be able to share insights into their quality assurance programs. If not, this may be a sign the company does not want to share their QA standards or they do not value it enough to keep their entire team up-to-date. Either way, neither of those scenarios should be acceptable to pet parents. Hood, for example, regularly educates Redbarn team members—from sales and marketing to customer service and purchasing— on quality assurance programs. Redbarn is proud of our accomplishments in the QA space and wants to make sure everyone working within Redbarn’s headquarters and manufacturing facilities, in addition to pet parents, feels confident in the products we put out.
2. What questions should I ask a pet food manufacturer to learn about their quality assurance standards?
In a recent interview with Animal Wellness Magazine, Hood shared a list of questions for pet parents to ask when researching a company’s QA.
- Does your company own independent manufacturing facilities?
- If so, does the State Department of Agriculture, FDA and/or USDA regularly inspect it? If not, how do you monitor quality assurance standards and practices within the facility?
- What type of testing do you perform on your raw and finished products?
- Does your manufacturing facility have any certifications?
- Does your facility utilize an outside ISO accredited lab for additional testing, verifying your results?
- Does your facility follow HACCP (Hazard Analysis and Critical Control Points) Standards?
If you have any questions about any of the products or quality assurance best practices, feel free to customer service at 1-800-775-3849.
Did you find this information helpful? Let us know below in the comments! We love engaging with our #RedbarnFamily.